Taking a look at Grasshopper
- lewisbond1997
- Apr 29, 2021
- 2 min read
Updated: Jun 14, 2021

Grasshopper is a plug-in for Rhino that allows the user to input lines of code to complete complex logistical tasks that would be far less efficient or next to impossible otherwise. 'The program was created by David Rutten at Robert McNeel & Associated. Programs are created by dragging components onto a canvas.' Learning to use this tool has pushed my 3D modelling skill set to a higher professional level, hopefully increasing my employability as I prepare to enter industry.
Grasshopper was first introduced to me while researching possible ways to re-create the panelling for my model of the Heydar Aliyev Centre. Developing these skills through YouTube video tutorials such as, 'Rhino Panelling Tools Tutorial' by 'Rhino Grasshopper' and Panelling Tools in Grasshopper for Beginners' by 'How to Rhino.' Providing indicators to additional plugins specific to Grasshopper such as 'Lunchbox' which was purpose built to create panelling on the platform.
After reaching out to a few of these videographers through the comments section I have contacted one going by the name 3D Beast. With whom I have been able to discuss the most efficient coding techniques to achieve my desired form.
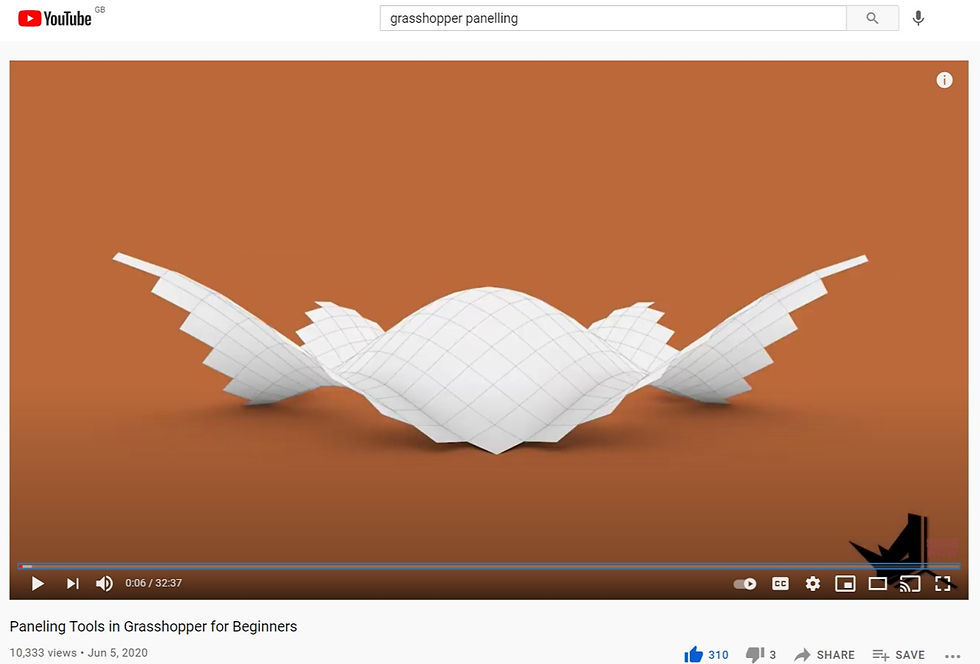

Conversations with 3D Beast

Lunchbox for Grasshopper
The initial code developed, whilst successful in creating panels of the desired size and contouring, saw issues. The panels needed shadow gaps to maintain detail. Without these the model would look like a a blocky version of the building. Whilst this was a desired feature of my model the original code prevented 3D printing as the sections were not one solid, but rather a collection of individual panels detached from one another.
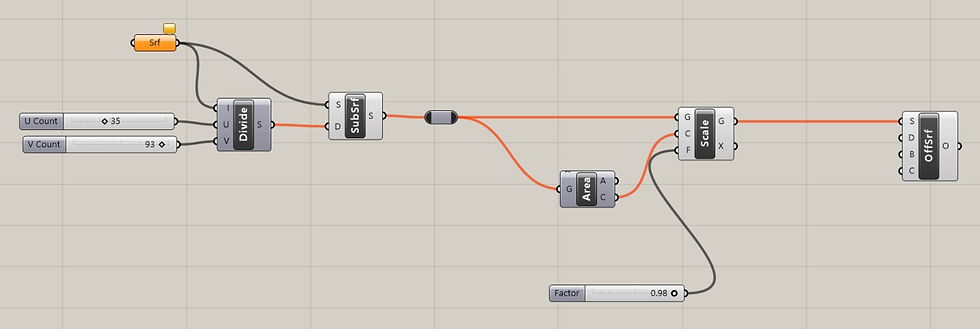

Original Grasshopper (top) code with non - 3D printable shadow gap example (bottom)
Beginning to brainstorm ideas for a solution I contacted Matthew Stewart an Alumni from my Modelmaking course at Arts University Bournemouth who had experience with Grasshopper from his FMP the year before. Our conversation resulted in the idea to create a series of pipes along the panelling joints to be boolean differenced, resulting in the desired 3D printable solid with all panelling detail maintained.


Developed Grasshopper code with all issues resolved (top) (repeated and adjusted for each component) (bottom)

Example of piping pre boolean difference

Boolean differenced piping creating shadow gaps as 3D printable components
Some advice on processing power and computation time reduction for Grasshopper:
Whilst an extremely powerful modelling tool it requires a large amount of processing power. Something that led to long waiting times for Rhino to complete basic boolean tasks. As the project has developed, I attempted to find ways to reduce pressure on my computer. Such as redirecting power from my graphics card to take some of the strain. Whilst this didn't work the most effective tool for quickly completing tasks appears to be breaking down the project into as may manageable components and apply the code to each one individually whilst hiding the rest. This results in a greatly decreased waiting time.
Comments